NEWS & EVENTS
企業精益改善的原點是什麼?
June 27,2023
企業精益改善的原點是什麼?
原創 精益 馮文翰 健峰管理技術培訓學校 點擊查看原文
企業精益改善的原點是什麼?
當別人拋出這個問題時,我們的腦海中浮現的第一個答案是什麼?
先不要回答,然後把答案放在我們的小腦袋瓜裡。
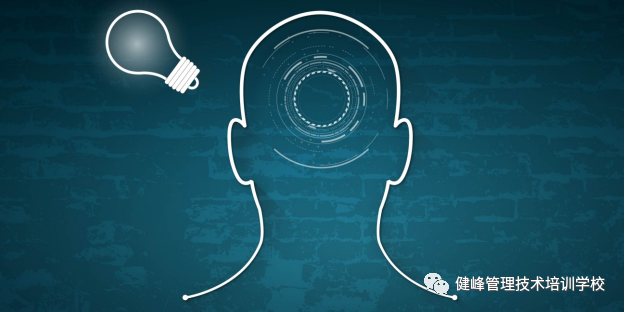
我們先看一個英國報社所出的高額獎金有獎徵答,看完後再想想答案有沒有變化。
題目是:
有一個充氣不足的熱氣球上,載著三位關係世界興亡命運的科學家。
第一位是環保專家,他的研究可拯救無數人們,免於因環境污染而面臨死亡的惡境。
第二位是核子專家,他有能力防止全球性的核子戰爭,使地球免於遭受滅亡的絕境。
第三位是糧食專家,他能在不毛之地,運用專業知識成功地種植食物,使幾千萬人脫離饑荒而亡的命運。
此刻熱氣球即將墜毀,必須丟出一個人以減輕載重,使其餘的兩人得以活存,請問該丟下哪一位科學家?
最高獎金得獎的小男孩:最胖的丟下去
看到這個答案,是不是有一種恍然大悟的感覺? 準確的判斷力是一種生存的本能,有時太多人被後天環境或人爲等等的影響,漸漸懷疑起自己的判斷力是否是正確的,自然引發出不必要的思考迴盪在腦海中,進而影響了自己最初的判斷,造成了不必要的錯誤與延宕。
試著把思緒淨空吧!渴了就是要喝水嘛!何必因爲一堆原因改喝了咖啡或飲料呢?況且飲料不僅不解渴,喝多了還對身體產生負擔~你說是不是?
仔細想想精益角度不就是遇到什麼問題就改什麼嗎?
所以企業精益改善的原點是什麼?在企業精益改善中,原點就是滿足客戶的需求,用最少的資源創造更大的價值。因此什麼是有價值的,什麼就是我們應該聚焦並且改善的。
精益生產的存在是跟大批量生產相反的,精益生產(Lean Production)是由美國麻省理工學院(MIT)的研究小組,在豐田公司用了5年時間全面總結生產方式後提出來的。
特別注重客戶需求、消除浪費、降低成本;其焦點是識別整個價值流,使價值增值流動並應用顧客拉動系統,使價值增值行爲在最短的時間內流動,創造更大的價值,並不斷地消除浪費,在穩定的需求環境下以最低的成本及時交付高質量的產品。在著作《精益思想》中提出精益管理五原則,顧客定義價值、定義價值溪流、價值流動化、由客戶需求拉動、持續改善,追求完美。精益管理的核心思想可概括爲消除浪費、創造價值。
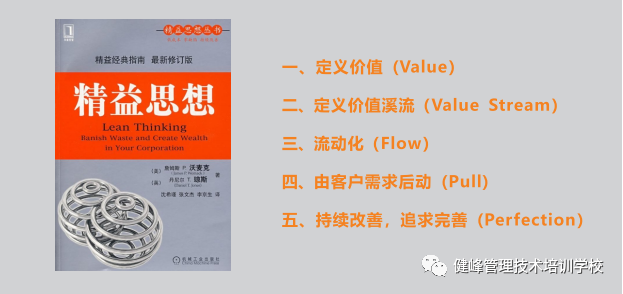
精益管理是精益生產理論的擴展,是精益思想在企業各層面的深入應用,精益管理是以精益思想爲指導、以持續追求浪費最小、價值最大的生產方式和工作方式爲目標的管理模式。
顧客定義價值
顧客定義價值就是以客戶的觀點來確定企業從設計、生產到交付的全部過程,實現客戶需求的最大滿足。以客戶的觀點定義價值還必須將生產的全過程的多餘浪費降到最低,不將額外的成本轉嫁給用戶。
精益價值觀將商家和客戶的利益統一起來,而不是過去那種對立的觀點。以客戶爲中心的價值觀來審視企業的產品設計、製造過程、服務項目就會發現太多的浪費,從不滿足客戶需求到過分的功能和多餘的非增值消耗。
當然,消滅這些浪費的直接受益者既是客戶也是商家。與之對照的是,企業過去的價值觀都是以自己爲中心的。完全由商家設計和製造的產品、完全由商家設計好的服務項目,大吹大擂那些目的在於增加贏利的、額外的、甚至是「畫蛇添足」的功能,並不一定是用戶所需要的、或必需的。
最後將大量的浪費以成本的方式轉嫁給了用戶。而用戶享受到的僅僅是爲實現這個轉嫁的殷勤。
定義價值溪流
價值溪流是指從原材料轉變爲成品、並賦予價值的全部活動。這些活動包括:從概念到設計和工程、到投產的技術過程,從訂單處理、計畫到送貨的資訊過程,和從原材料到產品的物質轉換過程,以及產品全生命週期的支持和服務過程。
精益思想-定義價值溪流的含義是在價值溪流中找到那些是真正增值的活動、那些是可以立即去掉的不增值活動。精益思想將所有業務過程中消耗了資源而不增值活動叫做浪費。定義價值溪流就是發現浪費和消滅浪費。
定義價值溪流的方法是「價值溪流分析 Value Stream map Analysis」——首先按產品族爲單位畫出當前的價值流圖,再以客戶的觀點分析每一個活動的必要性。價值溪流分析成爲實施精益思想最重要的工具。
價值溪流並不是從自己企業的內部開始的,多數價值流都向前延伸到供貨商,向後延長到向客戶交付的活動。按照最終用戶的觀點全面的考察價值流、尋求全過程的整體最佳,特別是推敲部門之間交接的過程,往往存在著更多的浪費。
價值流動化
如果正確的確定價值是精益思想的基本觀點、識別價值流是精益思想的準備和入門的話,「流動」和「拉動」則是精益思想實現價值的中堅。精益思想要求創造價值的各個活動(步驟)流動起來,強調的是不間斷地「流動」。
「價值流」本身的含義就是「動」的,但是由於根深蒂固的傳統觀念和做法,如部門的分工(部門間交接和轉移時的等待)、大批量生產(工具機旁邊等待的在製品)等等阻斷了本應動起來的價值流。
精益將所有的停滯作爲企業的浪費,「所有的人都必須和部門化的、批量生產的思想做鬥爭」,用持續改進、JIT、單件流等方法在任何批量生產條件下創造價值的連續流動。當然,使價值流流動起來,必需具備必要的環境條件。這些條件是:過失、廢品和返工都造成過程的中斷、迴流。
實現連續的流動要求每個過程和每個產品都是正確的。全面質量管理和後來的6 Sigma都成爲精益思想的重要組成部分。環境、設備的完好性是流動的保證。5S、TPM全員生產保全都是價值流動的前提條件之一。有正確規模的人力和設備能力,避免瓶頸造成的阻塞。
由客戶需求拉動
「拉動」就是按客戶的需求投入和產出,使用戶精確的在他們需要的時間得到需要的東西。實行拉動以後用戶或製造的下游就像在超市的貨架上一樣地取到他們所需要的東西,而不是把用戶不太想要的產品強行推給用戶。拉動原則由於生產和需求直接對應,消除了過早、過量的投入,而減少了大量的庫存和現場在製品,大量的壓縮了提前期。拉動原則更深遠的意義在於企業具備了當用戶一旦需要,就能立即進行設計、計畫和製造出用戶真正需要的產品的能力,最後實現拋開預測,直接按用戶的實際需要進行生產。
實現拉動的方法是實行JIT生產和單件流。當然,JIT和單件流的實現最好採用單元佈置,對原有的製造流程做深刻的改造。流動和拉動將使產品開發時間減少、訂貨週期減少、生產週期降低,這對傳統的改進來說簡直是個奇蹟。
持續改善,追求完美
奇蹟的出現是由於上述 4 個原則相互作用的結果。改進的結果必然是價值流動速度顯著的加快。這樣就必須不斷地用價值流分析方法找出更隱蔽的浪費,作進一步的改進。這樣的良性循環成爲趨於盡善盡美的過程。
精益製造的目標是:「通過持續改善,追求完美的價值創造過程(包括設計、製造和對產品或服務整個生命週期的支援)爲用戶提供追求完美的價值」。
「100分的完美」是永遠達不到的,但持續地對「100分的完美」追求,將造就一個永遠充滿活力、不斷進步的企業。由顧客確定產品價值結構。
還是那句老話 : 沒有最好,只有更好~
原創 精益 馮文翰 健峰管理技術培訓學校 點擊查看原文
企業精益改善的原點是什麼?
當別人拋出這個問題時,我們的腦海中浮現的第一個答案是什麼?
先不要回答,然後把答案放在我們的小腦袋瓜裡。
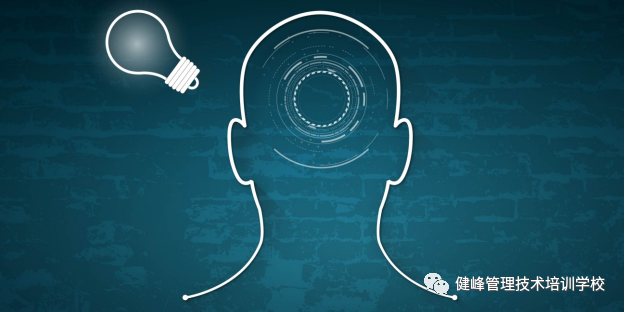
我們先看一個英國報社所出的高額獎金有獎徵答,看完後再想想答案有沒有變化。
題目是:
有一個充氣不足的熱氣球上,載著三位關係世界興亡命運的科學家。
第一位是環保專家,他的研究可拯救無數人們,免於因環境污染而面臨死亡的惡境。
第二位是核子專家,他有能力防止全球性的核子戰爭,使地球免於遭受滅亡的絕境。
第三位是糧食專家,他能在不毛之地,運用專業知識成功地種植食物,使幾千萬人脫離饑荒而亡的命運。
此刻熱氣球即將墜毀,必須丟出一個人以減輕載重,使其餘的兩人得以活存,請問該丟下哪一位科學家?
最高獎金得獎的小男孩:最胖的丟下去
看到這個答案,是不是有一種恍然大悟的感覺? 準確的判斷力是一種生存的本能,有時太多人被後天環境或人爲等等的影響,漸漸懷疑起自己的判斷力是否是正確的,自然引發出不必要的思考迴盪在腦海中,進而影響了自己最初的判斷,造成了不必要的錯誤與延宕。
試著把思緒淨空吧!渴了就是要喝水嘛!何必因爲一堆原因改喝了咖啡或飲料呢?況且飲料不僅不解渴,喝多了還對身體產生負擔~你說是不是?
仔細想想精益角度不就是遇到什麼問題就改什麼嗎?
所以企業精益改善的原點是什麼?在企業精益改善中,原點就是滿足客戶的需求,用最少的資源創造更大的價值。因此什麼是有價值的,什麼就是我們應該聚焦並且改善的。
精益生產的存在是跟大批量生產相反的,精益生產(Lean Production)是由美國麻省理工學院(MIT)的研究小組,在豐田公司用了5年時間全面總結生產方式後提出來的。
特別注重客戶需求、消除浪費、降低成本;其焦點是識別整個價值流,使價值增值流動並應用顧客拉動系統,使價值增值行爲在最短的時間內流動,創造更大的價值,並不斷地消除浪費,在穩定的需求環境下以最低的成本及時交付高質量的產品。在著作《精益思想》中提出精益管理五原則,顧客定義價值、定義價值溪流、價值流動化、由客戶需求拉動、持續改善,追求完美。精益管理的核心思想可概括爲消除浪費、創造價值。
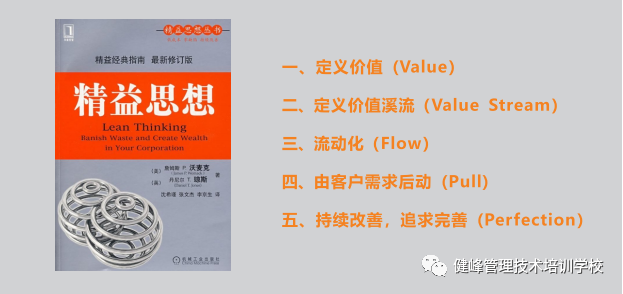
精益管理是精益生產理論的擴展,是精益思想在企業各層面的深入應用,精益管理是以精益思想爲指導、以持續追求浪費最小、價值最大的生產方式和工作方式爲目標的管理模式。
顧客定義價值
顧客定義價值就是以客戶的觀點來確定企業從設計、生產到交付的全部過程,實現客戶需求的最大滿足。以客戶的觀點定義價值還必須將生產的全過程的多餘浪費降到最低,不將額外的成本轉嫁給用戶。
精益價值觀將商家和客戶的利益統一起來,而不是過去那種對立的觀點。以客戶爲中心的價值觀來審視企業的產品設計、製造過程、服務項目就會發現太多的浪費,從不滿足客戶需求到過分的功能和多餘的非增值消耗。
當然,消滅這些浪費的直接受益者既是客戶也是商家。與之對照的是,企業過去的價值觀都是以自己爲中心的。完全由商家設計和製造的產品、完全由商家設計好的服務項目,大吹大擂那些目的在於增加贏利的、額外的、甚至是「畫蛇添足」的功能,並不一定是用戶所需要的、或必需的。
最後將大量的浪費以成本的方式轉嫁給了用戶。而用戶享受到的僅僅是爲實現這個轉嫁的殷勤。
定義價值溪流
價值溪流是指從原材料轉變爲成品、並賦予價值的全部活動。這些活動包括:從概念到設計和工程、到投產的技術過程,從訂單處理、計畫到送貨的資訊過程,和從原材料到產品的物質轉換過程,以及產品全生命週期的支持和服務過程。
精益思想-定義價值溪流的含義是在價值溪流中找到那些是真正增值的活動、那些是可以立即去掉的不增值活動。精益思想將所有業務過程中消耗了資源而不增值活動叫做浪費。定義價值溪流就是發現浪費和消滅浪費。
定義價值溪流的方法是「價值溪流分析 Value Stream map Analysis」——首先按產品族爲單位畫出當前的價值流圖,再以客戶的觀點分析每一個活動的必要性。價值溪流分析成爲實施精益思想最重要的工具。
價值溪流並不是從自己企業的內部開始的,多數價值流都向前延伸到供貨商,向後延長到向客戶交付的活動。按照最終用戶的觀點全面的考察價值流、尋求全過程的整體最佳,特別是推敲部門之間交接的過程,往往存在著更多的浪費。
價值流動化
如果正確的確定價值是精益思想的基本觀點、識別價值流是精益思想的準備和入門的話,「流動」和「拉動」則是精益思想實現價值的中堅。精益思想要求創造價值的各個活動(步驟)流動起來,強調的是不間斷地「流動」。
「價值流」本身的含義就是「動」的,但是由於根深蒂固的傳統觀念和做法,如部門的分工(部門間交接和轉移時的等待)、大批量生產(工具機旁邊等待的在製品)等等阻斷了本應動起來的價值流。
精益將所有的停滯作爲企業的浪費,「所有的人都必須和部門化的、批量生產的思想做鬥爭」,用持續改進、JIT、單件流等方法在任何批量生產條件下創造價值的連續流動。當然,使價值流流動起來,必需具備必要的環境條件。這些條件是:過失、廢品和返工都造成過程的中斷、迴流。
實現連續的流動要求每個過程和每個產品都是正確的。全面質量管理和後來的6 Sigma都成爲精益思想的重要組成部分。環境、設備的完好性是流動的保證。5S、TPM全員生產保全都是價值流動的前提條件之一。有正確規模的人力和設備能力,避免瓶頸造成的阻塞。
由客戶需求拉動
「拉動」就是按客戶的需求投入和產出,使用戶精確的在他們需要的時間得到需要的東西。實行拉動以後用戶或製造的下游就像在超市的貨架上一樣地取到他們所需要的東西,而不是把用戶不太想要的產品強行推給用戶。拉動原則由於生產和需求直接對應,消除了過早、過量的投入,而減少了大量的庫存和現場在製品,大量的壓縮了提前期。拉動原則更深遠的意義在於企業具備了當用戶一旦需要,就能立即進行設計、計畫和製造出用戶真正需要的產品的能力,最後實現拋開預測,直接按用戶的實際需要進行生產。
實現拉動的方法是實行JIT生產和單件流。當然,JIT和單件流的實現最好採用單元佈置,對原有的製造流程做深刻的改造。流動和拉動將使產品開發時間減少、訂貨週期減少、生產週期降低,這對傳統的改進來說簡直是個奇蹟。
持續改善,追求完美
奇蹟的出現是由於上述 4 個原則相互作用的結果。改進的結果必然是價值流動速度顯著的加快。這樣就必須不斷地用價值流分析方法找出更隱蔽的浪費,作進一步的改進。這樣的良性循環成爲趨於盡善盡美的過程。
精益製造的目標是:「通過持續改善,追求完美的價值創造過程(包括設計、製造和對產品或服務整個生命週期的支援)爲用戶提供追求完美的價值」。
「100分的完美」是永遠達不到的,但持續地對「100分的完美」追求,將造就一個永遠充滿活力、不斷進步的企業。由顧客確定產品價值結構。
還是那句老話 : 沒有最好,只有更好~